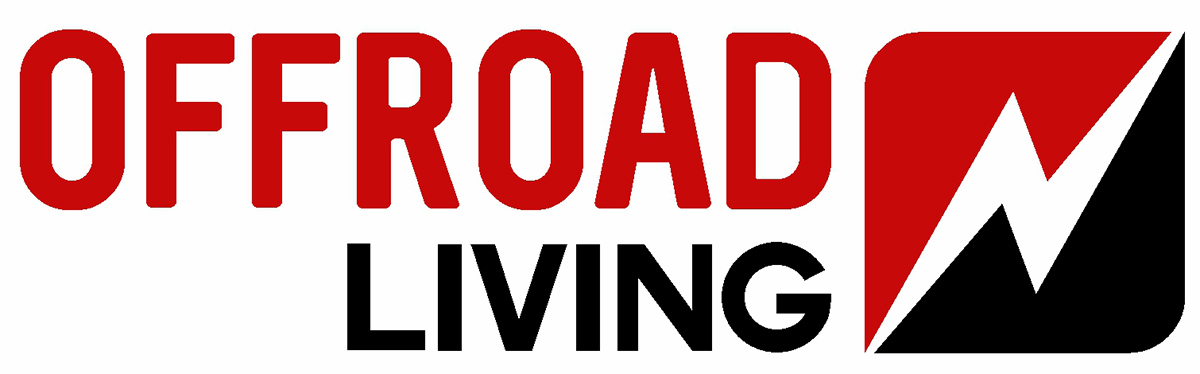
OFFROAD LIVING PRIVACY AND CREDIT REPORTING POLICY
1. About our Privacy and Credit Reporting Policy
1.1 This policy was last modified on 24 June 2021.
1.2 The privacy of your Personal Information is important to JKG Management and Investments Pty Ltd (ACN 161 507 106), trading as Offroad Living (we, us, our, Offroad Living). We respect your rights to privacy and rights under the Privacy Act and are committed to complying with the requirements of Privacy Legislation in the collection and handling of your Personal Information.
1.3 This policy explains how we collect and handle your Personal Information and Credit Related Information and describes the kinds of Personal Information and Credit Related Information we collect, use and disclose, and our purposes for doing so. This policy also explains the choices you have regarding our use of your Personal Information, your ability to access or correct that information and how you may complain should you believe we have breached our privacy obligations.
1.4 Please read this Privacy and Credit Reporting Policy carefully. Please contact us if you have any questions – our contact details are at the end of this policy.
1.5 By providing Personal Information to us, you consent to our collection, use and disclosure of your Personal Information in accordance with this Privacy and Credit Reporting Policy and any other agreement or arrangement between us. If you do not wish to provide your Personal Information to us, then you do not have to do so. However, it may affect our ability to provide services to you.
1.6 This policy applies to your use of our Website as well as your other dealings and engagements with us and sets out how and why we collect your Personal Information and Credit Related Information during your interactions with us. For the avoidance of doubt and unless stated otherwise, this policy will govern our collection of your Personal Information and Credit Related Information irrespective of the forum.
TAKE NOTICE THAT YOUR CONTINUED USAGE OF OUR WEBSITE AND/OR SERVICES WILL BE TAKEN TO INDICATE YOUR ACCEPTANCE OF THE TERMS OF THIS PRIVACY AND CREDIT REPORTING POLICY INSOFAR AS IT RELATES TO OUR WEBSITE.
1.7 This policy is not intended to cover categories of information that are not contemplated by the Privacy Legislation.
2. What is Personal Information?
2.1 Personal Information is information or an opinion, whether true or not, and whether recorded in a material form or not, about an individual whose identity is apparent, or can reasonably be ascertained, from the information or opinion.
3. Why we collect Personal Information
3.1 We collect Personal Information so that we can provide you with products and services and better your experience with us. We only collect Personal Information if it is reasonably necessary for us to carry out our functions and activities.
3.2 The purposes for which we collect, hold and use your Personal Information include:
(a) to deliver products and services to you;
(b) to respond to individual’s and company’s requests;
(c) in connection with your attendance or participation in functions, events or activities which we are involved in;
(d) to manage our relationship with you, evaluate our business performance and build our customer database;
(e) to provide you with information about our products, services, functions, events or activities;
(f) to process transactions;
(g) to enable you to participate in a promotion, competition, survey and / or enable you to subscribe to mailing lists/newsletters and interact or follow our social media pages, including Twitter, Facebook and Instagram;
(h) to provide you with aftermarket services, such as seeking your feedback, addressing any further requests you may have in connection with our services;
(i) to conduct research, compile or analyse statistics relevant to the operations of our business;
(j) to facilitate our internal business operations, including fulfilment of any legal and regulatory requirements;
(k) to create backups of our business records;
(l) to maintain a customer database or similar record;
(m) for direct marketing purposes as set out below; and
(n) to manage our Website operated in conjunction with our business, including analysing data collected from our Website concerning site visits and activities of users on our Website. This helps us run our Website more efficiently and give you a better experience online. We use information from third party services such as Google Analytics to help further improve your experience in using our Website.
3.3 We may also use your Personal Information for other purposes not listed above but this will be made clear to you at the time we collect your Personal Information.
3.4 We may use Credit Related Information that we collect and hold for the purpose of:
(a) deriving scores or ratings summarising your credit risk, which we may use as a factor in determining whether to provide credit to you;
(b) establishing and managing our relationship with you;
(c) exercising our rights and obligations;
(d) performing any administrative operations;
(e) collecting payments and other enforcement activities;
(f) to participate in the credit reporting system and provide information to a CRB as permitted by Part IIIA of the Privacy Act and the Credit Reporting Code;
(g) to meet legal and regulatory requirements;
(h) to protect you and us from fraud; and
(i) to respond to any queries or complaints you may have.
3.5 Some Credit Related Information may only be used or disclosed under the Privacy Act for some of these purposes or in some circumstances.
3.6 We may contact you by a variety of measures including, but not limited to telephone, email, SMS or mail.
4. What kinds of Personal Information we collect
4.1 The kinds of Personal Information we collect will depend on the type of interaction you have with us. Generally, the kinds of Personal Information we collect may include:
(a) your name, address (postal and residential), place of employment, occupation, email address, telephone number(s), date of birth and gender;
(b) your individual preferences in respect of the services we provide you;
(c) details of your device you have used to access any part of our website;
(d) demographic information;
(e) details as to whether you have taken up any products or offerings we have made;
(f) whether you have a connection with others whose Personal Information we may collect or hold;
(g) what, how and when you have dealt with us or expressed an interest in buying from us;
(h) any stated preferences for our products or services you have provided to us; and
(i) credit card and direct debit details for your bank account should you elect to pay us via this method.
4.2 In the course of providing you with professional services, we may also have a need to collect additional Personal Information (for instance, financial details or credit information).
5. Credit Related Information we collect
5.1 The Credit Related Information we may collect and hold varies. Information can include but is not limited to:
(a) details of credit (including the name of each relevant credit provider) that you have applied for, the type and amount of that credit and the fact that a credit provider, mortgage insurer or trade insurer has sought information about you from a CRB in relation to an application;
(b) credit liability information, being details of credit that you have or had including the credit provider, the type of credit, the day on which it was entered into, terms or conditions that relate to the repayment of the amount of credit, the maximum amount of credit available and the day on which the credit is terminated or otherwise ceases;
(c) default information, which includes details of payments (over $150) more than 60 days overdue in relation to credit which you, as a borrower, have failed to make;
(d) payment information, which includes details of the date on which you have paid overdue amounts that were previously recorded as default information with a CRB;
(e) whether in another credit provider’s opinion you have committed a serious credit infringement;
(f) new arrangement information which includes a statement that the terms or conditions of your credit (in relation to which default information or a serious credit infringement has been disclosed to a CRB) have been varied or that you have been provided with new credit;
(g) court proceedings information, which includes information about a judgement against you in proceedings that relate to any credit that has been provided to, or applied for, by you;
(h) personal insolvency information, which includes information about any procedures under the Bankruptcy Act which relate to you;
(i) certain publicly available information;
(j) scores and other information relating to your credit worthiness which is derived by CRBs wholly or partly on the basis of the information above; and
(k) certain administrative information, such as account numbers.
5.2 In most cases, if we do not collect the Credit Related Information we require, then we will be unable to provide credit to you.
6. How we disclose Personal Information
6.1 We may disclose your Personal Information insofar as reasonably necessary for the purposes set out in this Privacy and Credit Reporting Policy. Personal Information and Credit Related Information is only disclosed to a third party when it is required for the delivery of our services.
6.2 We may disclose Personal Information collected from you:
(a) to third party operators of online stores which we sell our products through, including eBay.com and other similar sites;
(b) to our related entities, third party suppliers, consultants, employees, agents, contractors, sponsors, government agencies or other third parties to satisfy the purposes for which the information was collected for (as outlined in clause 3 of this policy) or for another purpose if that other purpose is closely related to the primary purpose of collection and an individual would reasonably expect us to disclose the information for that secondary purpose;
(c) when your authorised representative, such as an accountant or lawyer, contact us in connection with providing you with services;
(d) if the disclosure is requested by a government agency or the courts and we are obliged to comply;
(e) to CRBs, as permitted by law;
(f) to any other person, with your consent (express or implied); and
(g) to any person to whom our assets or business (or any part thereof) is transferred to.
6.3 In addition to the above, we will disclose your Personal Information if we are required to do so under law or if the disclosure is made in connection with either the normal operation of our business in a way that you might reasonably expect, for example to process an insurance claim, or if such disclosure is incidental to IT services being provided to our business, or in connection with any insurance or warranty claim or for the resolution of any dispute that arises between you and us. This disclosure may involve your Personal Information being transmitted overseas.
6.4 Organisations providing professional services to us are required to keep those dealings and Personal Information provided by us confidential unless they are required to disclose such information by statute or law.
6.5 In the case of contracted service providers, we may disclose Personal Information to the contracted service provider and the contracted service provider may in turn provide us with Personal Information collected from you in the course of providing the relevant products or services.
6.6 We may also disclose Credit Related Information about you to CRBs, other credit providers listed in your application or other permitted recipients of Credit Related Information. We may disclose that information for the purposes of notifying CRBs or other credit providers of a default by you, ascertaining the status of credit provided to you by us where you are in default with other credit providers, assessing your credit worthiness, credit standing or credit capacity and responding to any queries or complaints you may have.
6.7 We may also disclose your Personal Information if you choose to participate in online or “app” based service offerings whereby your Personal Information may be disclosed to and stored in software which is operated by a third party intermediary as part of your dealings with us. Personal Information disclosed in this may be transmitted offshore, including to the United States of America. When you provide your Personal Information to us, you consent to the disclosure of your Personal Information to recipients outside of Australia and acknowledge that we are not required to ensure that such overseas recipients comply with the Privacy Legislation in relation to your Personal Information. We will take reasonable steps to ensure any overseas recipient we deal with Personal Information in a manner consistent with the APPs.
6.8 In the event of a restructure or sale of our business (or part of our business), we may disclose Personal Information to the buyer without your consent subject to compliance with the Privacy Legislation. If we sell the business and the sale is structured as a share sale, you acknowledge that this will not constitute the ‘transfer’ of Personal Information.
6.9 We will not sell, trade or rent your Personal Information to any third parties for marketing purposes without your consent.
6.10 Where we disclose your Personal Information or Credit Related Information to a third party, we will request that the third party complies with this policy when handling your Personal Information or Credit Related Information.
7. How we collect and store data and transmit Personal Information
7.1 Generally, we collect Personal Information and Credit Related Information directly from you where reasonable and practicable.
7.2 We usually collect and store information in paper, physical and electronic form provided by you in person or when you communicate with us by telephone, email, web-based form, letter, facsimile or other means, including:
(a) when you contact us over the phone;
(b) when we provide you with our services via telephone, email or our website;
(c) when we provide you with assistance or support for our products or services;
(d) when you participate in our functions, events, activities or social media pages;
(e) when you request that we provide you with information concerning our products or services; and
(f) if you complete any forms requesting information from you, complete any survey or provide feedback to us concerning our products or services.
7.3
7.4 We may receive Personal Information and Credit Related Information from third parties, such as other credit providers, your financial institution, CRBs, publicly available information and our related companies. If we do, we will protect it as set out in this Privacy and Credit Reporting Policy. We will only collect your Personal Information and Credit Related Information from third parties if it is unreasonable or impractical to collect the necessary information directly from you or if we are otherwise permitted to do so.
7.5 Please note that we use our own and third party computer servers including our website hosts, data backups and payment gateway(s), which may be located overseas and as such your Personal Information will likely be stored and transmitted overseas as part of the normal operation of our business.
7.6 We will endeavour to take all reasonable steps to keep secure and protect any Personal Information and Credit Related Information which we hold about you, including: (a) securing our physical premises and digital storage media; (b) placing password protection and access control over our information technology systems and databases to limit access and protect electronic information from unauthorised interference, access, modification and disclosure; and (c) taking regular back-ups of our electronic systems.
7.7 Notwithstanding that we will take all reasonable steps, data transmission over the internet is never guaranteed to be completely secure. In the circumstances, we do not warrant the security of any information you transmit to us or from any online services.
7.8 We will take reasonable steps to destroy or permanently de-identify Personal Information that is no longer needed for any purpose that is permitted by the Privacy Act.
8. Website and cookies
8.1 We also collect information from your computer automatically when you browse our Website. This information may include:
(a) the date and time of your visit;
(b) your domain;
(c) locality;
(d) operating system;
(e) the server your computer is using to access our Website;
(f) your browser and version number;
(g) search terms you have entered to find our Website or enter on our Website;
(h) pages and links you have accessed both on our Website and on other websites;
(i) the last website you have visited;
(j) the pages of our Website you access; and
(k) your IP Address.
8.2 Please note that it may be possible for us to identify you from information collected automatically from your visit(s) to our Website. If you have registered an account with us, we will able to identify you through your user name and password when you log into our website or any applications. Further, if you access our Website via links in an email we have sent you, we will be able to identify you.
8.3 We may use statistical analytics software tools such as Google Analytics and software known as cookies which transmit data to third party servers located overseas including in the United States of America. To our knowledge Google Analytics does not identify individual users or associate your IP Address with any other data held by Google.
8.4 If you do not wish to grant us the right to use cookies to gather information about you while you are using our Website, then you may elect to set your browser settings to disable cookies. This may cause parts of our Website to not function properly.
8.5 Please note that our Website may contain links to other websites, and your use of those websites is not covered by this Privacy and Credit Reporting Policy. We encourage you to review each website’s privacy policy.
9. Sensitive Information
9.1 We collect Sensitive Information about you in the form of health information when you complete our Health Questionnaire or when you notify us of an illness, injury or other matters.
9.2 We will only collect Sensitive Information about you if:
(a) you consent to the collection and the information is reasonably necessary for one or more of our functions or activities; or
(b) the collection is otherwise permitted under the Privacy Act.
9.3 We will only disclose your Sensitive Information if it is directly related to the primary purpose for which it was collected.
10. How we use Personal Information for direct marketing
10.1 We may contact you from time to time to inform you about existing and new products and services that we feel you may be interested in.
10.2 We will ensure that any e-mail that you are sent by us as direct marketing complies with the SPAM Act 2003 (Cth) and contain an ‘unsubscribe’ option so that you can remove yourself from any further marketing communications.
10.3 You can also call or write to us to request that your details be removed from our direct marketing list. We will endeavour to remove your details from our direct marketing list within a reasonable time (ordinarily 5 business days).
10.4 Our direct marketing list may be operated by software and servers located overseas and as such your Personal Information may be sent overseas as part of our marketing.
11. Use of government related identifiers
11.1 We will not use government related identifiers (such as driver’s licence numbers) as our own identifier of individuals. We will only use or disclose such identifiers in the circumstances permitted by the Privacy Act.
12. Not identifying yourself
12.1 Because of the nature of our business, it is impracticable to deal with you on an anonymous basis or using a pseudonym.
12.2 We may be able to provide you with limited information in the absence of your identifying yourself but generally we will be unable to provide you with services unless you have identified yourself.
13. How to access or correct your Personal Information or make an enquiry or complaint
13.1 If you wish to access or correct the Personal Information we hold about you, or make a complaint, please contact us in writing via our contact details below and will try to resolve your concerns as soon as possible.
13.2 If we consider it necessary in order to deal with your request, we may consult with a CRB or another credit provider.
13.3 In order to disclose information to you in response to a request for access we may require you to provide us with sufficient comfort as to your identity. There are exceptions under the Privacy Legislation which may affect your right to access your Personal Information – these exceptions include where (amongst other things):-
(a) access would pose a serious threat to the life, health or safety of any individual;
(b) access would have an unreasonable impact on the privacy of others;
(c) the request for access is frivolous or vexatious;
(d) the information relates to existing or anticipated legal proceedings between you and us and the information would not otherwise be accessible by the process of discovery;
(e) giving access would reveal the intentions of the entity in relation to negotiations with you;
(f) giving access would be unlawful;
(g) denying access is required or authorised by or under an Australia law or a court/tribunal;
(h) the information relates to commercial sensitive decision making process; or
(i) giving access would prejudice enforcement related action.
13.4 We may (depending on the request) charge you a fee to access the Personal Information, which we will inform you of at the time. There is no cost involved for you to make a correction request or for the correction of your information. All requests for Personal Information will be handled in a reasonable period of time (within 30 days after the request is made).
13.5 If you wish to have your Personal Information deleted, please contact us using the details above and we will take reasonable steps to delete the information (unless we are obliged to keep it for legal or auditing purposes).
13.6 If we cannot take reasonable steps to correct the information because such correction is not technically possible or would be impractical for us to perform, we may be unable to continue to provide services to you. In these cases, we will provide reasons for the denial of your correction request.
13.7 If we refuse to correct your Personal Information, you have the right to associate with the information a statement that the information is inaccurate, out of date, incomplete, irrelevant or misleading. We will take such steps that are reasonable in the circumstances to associate that statement with all records containing the relevant information.
13.8 We reserve the right to refuse to provide you with information that we hold about you, in certain circumstances set out in the Privacy Act. If we cannot provide access to your information, we will generally provide you with the reasons why and the mechanisms to complain about that refusal.
14. Making a complaint and how it will be handled.
14.1 In the event that you believe that there has been a breach of the Privacy Legislation, we invite you to contact us as soon as possible using our contact details below. We will promptly investigate your complaint and respond to you in writing setting out the outcome of our investigation, what steps we propose to take to remedy the breach and any other action we will take to deal with your complaint.
14.2 It would assist us to ensure we properly understand your complaint, and allow us to respond more promptly, if complaints are made in writing and include as much detail as possible.
14.3 We will deal with any complaint in a timely, effective and consistent manner. We will acknowledge the receipt of your complaint within 7 days, and endeavour to make a decision on the complaint within 30 days after it is received. If we need more time to resolve your complaint, then we will notify you as to the delay.
14.4 If you are not satisfied with our handling of a complaint or the outcome of a complaint you may make an application to the Office of the Australian Information Commissioner by visiting www.oaic.gov.au, emailing enquiries@oaic.gov.au or writing to GPO Box 5218 Sydney NSW 2001.
15. Updates to this Privacy and Credit Reporting Policy
15.1 This policy may be updated from time to time and the most up to date version will be published on our Website.
16. Enquiries
16.1 If you have any concerns of queries about our Privacy and Credit Reporting Policy, or if you would like more information about privacy-related issues, please contact us at: Privacy Officer JKG Management and Investments Pty Ltd PO Box 1457 Wangara DC, 6947, WA or by email to contact@offroadliving.com.au
17. Definitions used in this policy
CRB means credit reporting body as defined in the Privacy Act.
Credit Related Information means credit information and credit eligibility information as defined under the Privacy Act.
IP Address means a number automatically assigned to your computer and which is required when you are using the internet and which may be able to be used to identify you.
Personal Information has the meaning set out in the Privacy Act.
‘we’ ‘our’, ‘us’ and similar terms means JKG Management and Investments Pty Ltd, ACN 161 507 106, trading as Offroad Living.
Privacy Act means the Privacy Act 1988 (Cth) as amended from time to time.
Privacy Legislation means such laws as may place requirements on the handling of Personal Information under the Privacy Act and the Australian Privacy Principles.
Sensitive Information means information relating to a person’s racial or ethic origin, political opinions, religion, trade union or other professional or trade association membership, sexual orientation, criminal record, and health information about an individual.
‘You’, ‘your’ and similar terms means, as the context requires:
(a) you, during your usage of our Website;
(b) you, during your dealings with us as a customer;
(c) any agent providing your Personal Information to us; and/or
(d) any agent dealing with us on your behalf.
‘Website’ means www.offroadliving.com.au and other website as we may operate from time to time including our stores operated by third parties including eBay.